The industrial internet of things (IIoT) is a hot topic, but there seems to be much confusion as to just what bottom line benefits it might deliver to manufacturing organizations. Many look upon it as an untested group of technologies looking for applications, but this is not how we see things.
In Emerson’s view, the IIoT is a logical extension of the work we’ve been doing for years to deliver value to manufacturers. New technologies, particularly Microsoft Azure, help improve our IIoT solutions by simplifying implementations and reducing costs.
Let’s first look at bottom line reasons why manufacturers should look at IIoT solutions. According to our research, there is a $1 trillion opportunity for process plant operators if they move to the top quartile in terms of safety, reliability, production and emissions. Figure 1 shows how we arrived at that figure.

What does it mean to be in the top quartile?
- Reduction of recordable safety incidents by two-thirds
- Operating costs 20 percent lower thanks to 10 percent higher plant utilization
- Emissions and energy use drop by 30 percent
- Improved reliability cuts maintenance costs in half and increases plant availability by 4 percent.
These are impressive numbers, and here’s how the IIoT can make it happen.
Data Acquisition and Storage is the First Step
As shown in Figure 2, real-time data, analytics, advanced security and cloud services are the foundations of the IIoT in manufacturing. Tremendous amounts of real-time data have been collected in process plants for decades, dwarfing the amount of data collected in other sectors of the economy. A single large refinery might collect more than ten thousand data points per second. Recent developments in wireless sensing technology have made it much less expensive to collect manufacturing data, allowing plants to sense even more parameters of interest.
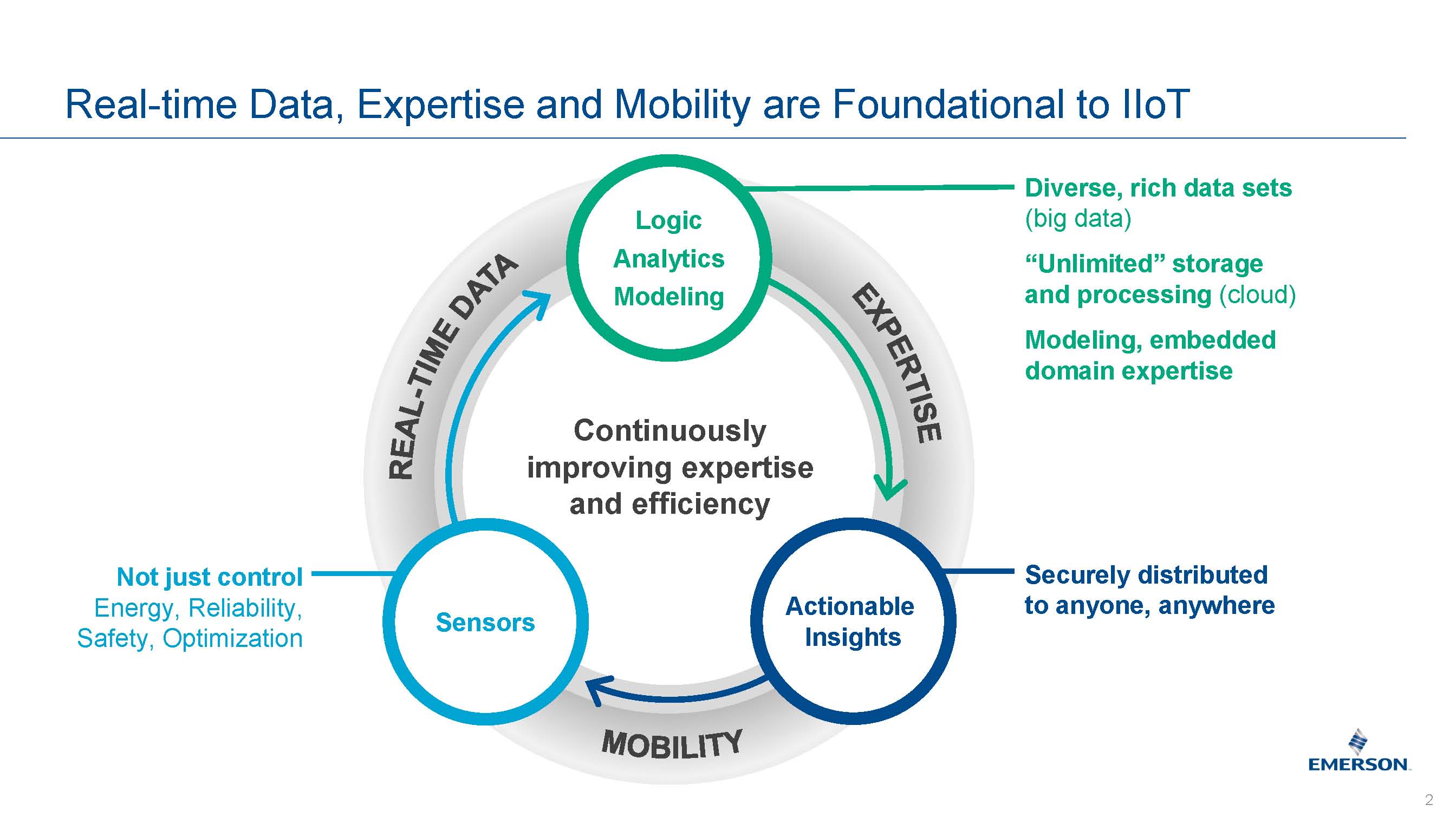
The first challenge is making all of this data available to those who need it, both within the plant and outside of its walls. In-plant data storage schemes are very well developed, with process data historians optimized to store very large amounts of time-series data in a very efficient manner. For data distribution outside the plant walls, the cloud is the answer in many cases due to its virtually unlimited data storage capability, which is being offered at ever lower prices. Cloud-based services such as Microsoft Azure can reliably store very large amounts at low cost.
Unlike on-premises data storage and distribution schemes, cloud-based services can be implemented very quickly and inexpensively, and capacity can be added incrementally and instantaneously as needed. Once data is uploaded to the cloud, advanced analytics can be run on the data. Additionally, these services also provide built-in data management tools to control access, for example, to make sure two different users aren’t trying to modify the same data simultaneously.
But acquiring data and getting it into the cloud are only the first step towards realizing the benefits of an effective IIoT implementation because data requires expertise in terms of interpretation to realize its full value.
Turning Data into Actionable Information
Manufacturing domain expertise is required to turn raw data into the kind of information required to move a process plant or other manufacturing facility to the top quartile. This expertise can be applied in one of three ways: locally, centralized by the manufacturer or through a third-party service.
Local experts on premises have been taking on this task for decades, but it has become increasingly difficult at many plants due to the retirement of skilled workers and ever-increasing amounts of data. This remains a very good solution for those facilities with the required onsite expertise, but two other approaches are finding favor.
The first is a centralized approach whereby a company with multiple plants locates its experts at one central location. Data is sent from each plant to the central location, via either a company or a cloud-hosted network. In the past, the networking cost for these types of IIoT implementations was very high, but cloud-based services have greatly reduced costs and installation time.
Cloud-based services are also at the heart of solutions where a third-party provider uses its experts to analyze data and turn it into actionable information. These third-party services can take on many forms, but in each case offer greater efficiencies than in-house solutions because they allow a group of experts to support many plants simultaneously. It may not be feasible for a plant, or even many plants within the same company, to keep a group of experts on staff, but third-party providers can afford to do so because their personnel and expertise are leveraged across many sites.
As with cloud-based services, manufacturing companies can purchase just the amount of domain expertise services needed, and can do so instantaneously and incrementally. Whereas internal resources must be added, trained and managed one person at a time, with a relatively high fixed cost per person, third-party services can be purchased as needed.
Third-party service providers typically offer multiple implementation options. One option is to analyze data and provide actionable information to the plant or plants. This can be done automatically through the cloud upon initiation by the service provider, with information sent from the third-party service provider to plant operators and engineers through their existing human-machine interface and asset management systems. Plant personnel can then take action as required to realize benefits.
A second option is for the third-party service provider to send personnel to the plant to act upon the information revealed by the analysis, working in conjunction with plant personnel. This option can allow plant personnel to focus on their main task, keeping the plant up and running, while working with the third-party service provider to make the incremental improvements required to move their facilities into the top quartile.
IIoT implementations have been used for decades in the process industries, but in the past intranets rather than the internet were the only practical networking technology. The advance of internet technologies, particularly cloud-based data storage and processing, has allowed plants to implement IIoT solutions much more quickly and at lower cost, speeding them on their journey to top quartile performance and millions of dollars in bottom-line benefits.
Bob Karschnia
VP & GM, Wireless
Emerson Automation Solutions