The Industrial IoT or IIoT, will represent a multi-trillion dollar opportunity by 2025 according to McKinsey & Company. This potential for energy savings, improved quality, increased throughput and other manufacturing benefits is driving conversations—but too often this dialog is focused on the IIoT infrastructure and technology instead of the applications which will deliver value.
The Industrial IoT (IIoT) helps automation facilities by connecting more sensors to control and monitoring systems to provide additional information to automatically improve the performance of process plants.
The IIoT:
- collects data from sensors (things), much more than ever before because of wireless technologies
- sends this data to control and monitoring systems, either local systems via plant wired and wireless networks (Intranets), or remote systems via the Internet
- interprets this data strategically, using Emerson’s process domain expertise to effectively analyze the data and turn it into actionable information
- presents actionable information to the right person, either plant personnel or Emerson experts
- results in performance improvements, when personnel take corrective action
Every day we see how even seemingly small operational improvements through applications can yield huge financial benefits for our customers through IIoT applications and for example,
Corrosion / erosion monitoring utilizes unique non-intrusive online sensor technology and wireless to ensure asset integrity by continuously monitoring for metal loss from corrosion or erosion in pipes, pipelines or vessels in the most difficult environments. This strengthens the ability to monitor the integrity of an oil & gas production, refining or power infrastructure in real-time in order to optimize their operations and maximize safety.
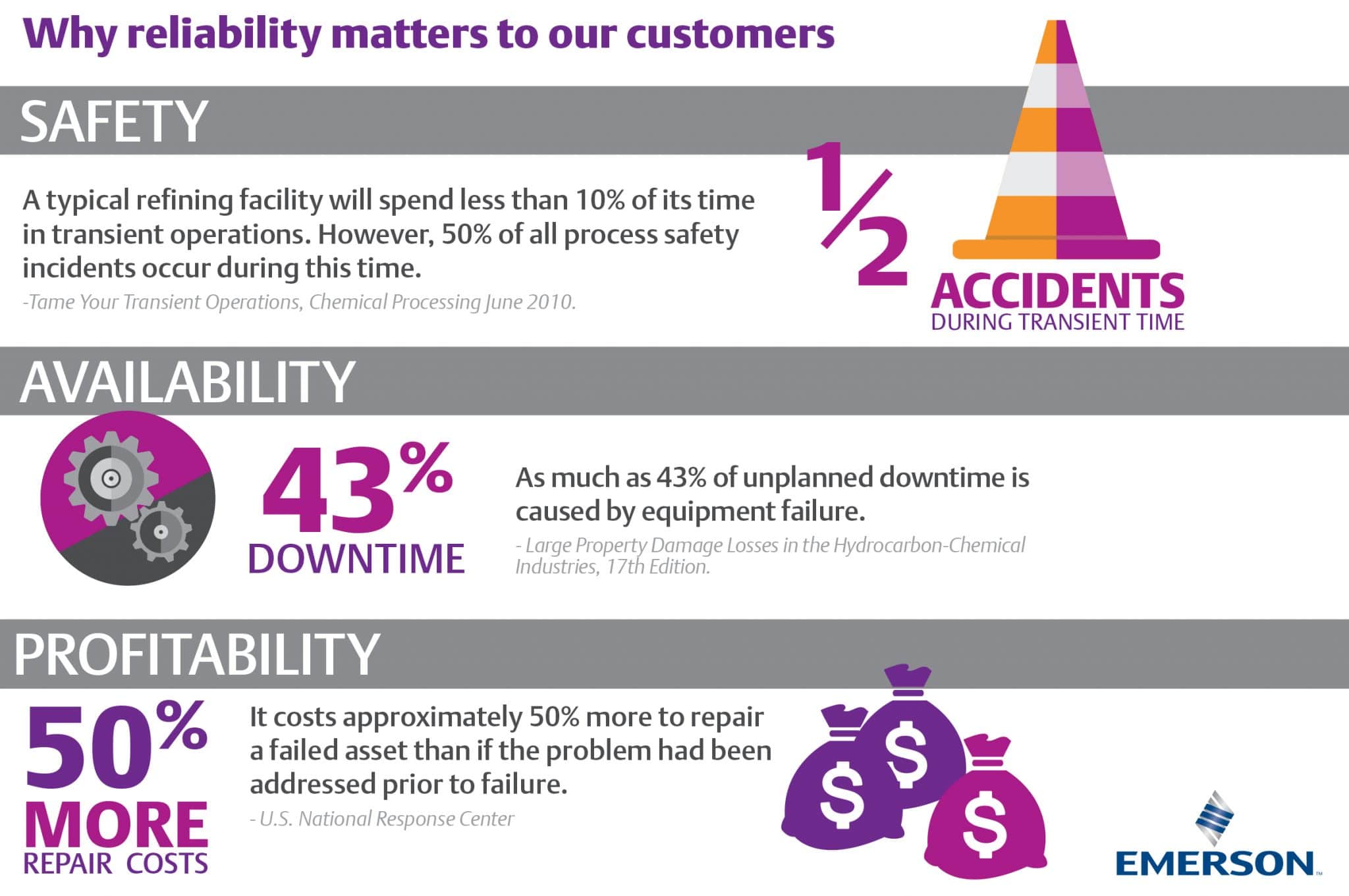
IIoT investments in wireless sensor systems increase reliability, directly impacting a refineries bottom line.
Stream trap monitoring utilizes innovative acoustic transmitters enabled through wireless, making it cost effective to monitor critical steam traps. Critical traps are those which waste a lot of energy if they fail open, or those which can cause significant damage to equipment if they fail closed. Online wireless monitoring of high value steam lines and critical steam traps cuts energy loss, prevents failures and increases uptime.
Pump health monitoring utilizes wireless flow, pressure, level, temperature, vibration and other transmitters which can help industrial facilities gain insights into equipment health for improved maintenance. At a fraction of the installed cost of wired transmitters, plants can replace manual rounds with on-line condition monitoring of pumps. This not only gives early indication of failure, but also avoids unnecessary maintenance on pumps that are healthy and removes the plant technician from the field.
So why haven’t all process automation manufacturers globally implemented applications like these given the proven financial benefits? One reason is that in the past, these inputs would have been wired from the sensing point, maybe a pump, to a control and monitoring system. Adding this wiring to an existing facility is usually a very expensive undertaking, and it often requires significant downtime, which isn’t an option as many refineries operate at or near full capacity.
But proven technologies allow these points of measurement to be added quickly and inexpensively with wireless sensors. These sensors are connected through a plant-wide wireless mesh network to control and monitoring systems. Wireless sensors allow points of measurement to be added at a fraction of the cost and time of their wired equivalents, and sensors not requiring process penetrations can be installed without any required downtime.
In short, adding wireless applications pervasively throughout the plant or refinery is the quick and cost-effective way to create a comprehensive plant-wide IIoT. These key measurement points coupled with data analysis and asset management systems improve operating performance, asset reliability and safety—resulting in higher profits.
To learn more visit www.Emerson.com
Bob Karschnia
Vice President and General Manager of Wireless
Emerson Automation Solutions